Introduction
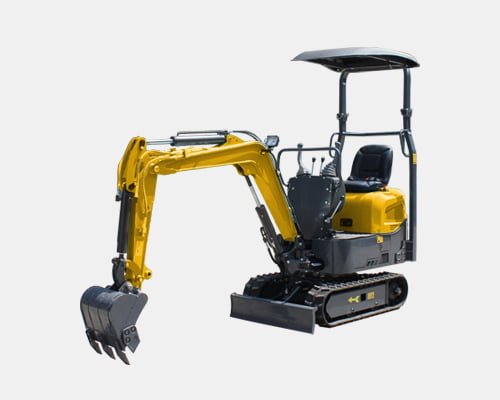
Mining excavators represent the backbone of large-scale extraction operations worldwide. In this comprehensive guide, we’ll delve into the fascinating world of mining excavators, exploring their significance, capabilities, and impact on the mining industry. From their evolution over the years to their role in various mining applications, we’ll uncover the intricacies of these powerful machines that drive the extraction of precious resources from the earth.
Evolution of Mining Excavators: From Humble Beginnings to Cutting-Edge Technology
Tracing the historical evolution of mining excavators unveils a remarkable journey marked by ingenuity and innovation. Initially conceived as rudimentary digging tools, early excavators were simple machines powered by human or animal labor, limited in their capabilities and efficiency. However, with the advent of the Industrial Revolution in the 19th century, significant strides were made in excavator design and technology. Steam-powered excavators emerged as pioneers, offering increased power and efficiency in excavation tasks.
Types and Varieties: Understanding the Diversity of Mining Excavators
When examining the various types of mining excavators, it becomes evident that each type possesses distinct features and capabilities tailored to specific mining applications.Each type of mining excavator—hydraulic excavators, rope shovels, and draglines—offers unique features and capabilities tailored to specific mining applications. Whether it’s the precision and versatility of hydraulic excavators, the high-volume excavation capabilities of rope shovels, or the sheer power and efficiency of draglines, mining companies have a diverse range of excavator options to choose from, allowing them to optimize their operations for maximum productivity and profitability.
Type of Mining Excavator | Features and Capabilities |
---|---|
Hydraulic Excavators | Precision, Versatility |
Rope Shovels | High-volume Excavation |
Draglines | Power, Efficiency |
Performance and Productivity: How Mining Excavators Drive Efficiency in Extraction Operations

Digging capacity refers to the volume of material an excavator can remove in a given period.Excavators with larger buckets and more powerful hydraulic systems typically have higher digging capacities, enabling them to excavate larger volumes of material in less time.Digging capacity refers to the volume of material an excavator can remove in a given period. It is influenced by factors such as the size and design of the excavator’s bucket, the power and efficiency of its hydraulic system, and the strength of its boom and arm components.
The skill and experience of the excavator operator have a significant impact on performance. A skilled operator can maximize the efficiency of the excavator, optimize cycle times, and minimize downtime due to operator error or mishaps.
Regular maintenance is essential to ensure the continued performance and reliability of mining excavators. Proper lubrication, inspection, and servicing of components such as hydraulic systems, tracks, and engines are critical to prevent breakdowns and downtime.
Applications Across the Mining Spectrum: From Open-Pit to Underground Operations
Exploring the myriad of mining applications in which excavators are indispensable unveils their versatile nature and adaptability across various environments and challenges. From open-pit mining to quarrying and underground operations, excavators play a pivotal role in facilitating extraction and material handling processes.
Open-Pit Mining: In open-pit mining, excavators are used extensively for tasks such as overburden removal, ore excavation, and loading of haul trucks. Their robust construction and high digging capacities make them ideal for handling large volumes of material efficiently. Excavators in open-pit mining are often equipped with large buckets and long booms to reach deep into the excavation pits, maximizing productivity and minimizing cycle times.
Quarrying: Excavators are essential in quarrying operations for tasks such as bench excavation, rock breaking, and material loading. In quarries, excavators may be equipped with specialized attachments such as rock buckets, hydraulic hammers, or ripper teeth to tackle hard and abrasive materials effectively. Additionally, excavators in quarrying applications may feature reinforced undercarriages and protective guarding to withstand the rugged terrain and harsh operating conditions common in quarry environments.
Underground Mining: In underground mining, excavators play a vital role in tasks such as shaft sinking, tunneling, and ore handling. Excavators used in underground mining are typically smaller and more compact than their open-pit counterparts to navigate the confined spaces and tight tunnels characteristic of underground environments. They may also feature enhanced maneuverability and specialized attachments for tasks such as mucking, scaling, and bolting in underground workings.
Innovations and Future Trends: The Next Frontier in Mining Excavator Technology
Delving into the realm of the latest innovations and technological trends shaping the future of mining excavators unveils a landscape brimming with promise and potential. As the mining industry continues to evolve, excavator manufacturers and technology providers are at the forefront of driving progress and innovation.
In summary, the future of mining excavators holds immense promise, driven by a convergence of technological innovation, sustainability imperatives, and industry demands. By embracing the latest advancements and pushing the boundaries of possibility, mining excavators are poised to play a pivotal role in shaping the future of the mining industry for generations to come.
Conclusion
Mining excavators represent the pinnacle of engineering excellence in the mining industry, driving efficiency, productivity, and progress in extraction operations worldwide. From their humble beginnings to their role as indispensable assets in modern mining, these machines continue to evolve and adapt to meet the challenges of the ever-changing mining landscape. As we look to the future, mining excavators will undoubtedly remain at the forefront of innovation, shaping the course of mining operations for generations to come.
FAQs
What are the main components of a mining excavator?
Mining excavators typically consist of a boom, stick (or arm), bucket, cab, tracks or wheels for mobility, hydraulic systems, and an engine. These components work together to enable the excavator to perform various tasks such as digging, loading, and dumping materials.
How do mining excavators differ from construction excavators?
While both mining and construction excavators share similarities in design and function, mining excavators are generally larger and more robust to withstand the demanding conditions of mining operations. They often have larger buckets, higher digging capacities, and reinforced structures to handle heavy-duty tasks in challenging environments.
What are the key considerations when selecting a mining excavator for a specific application?
When choosing a mining excavator, factors to consider include the type of material being excavated, the size and depth of the mining operation, the available budget, the required productivity, and the terrain conditions. It’s essential to select an excavator that is appropriately sized and equipped to handle the specific demands of the mining site.