Introduction
Excavator Parts: Unearthing the Essentials.In the construction and heavy machinery industry, excavators are true workhorses, playing a pivotal role in creating the world we know today. These powerful machines, often referred to as “diggers,” are responsible for moving earth and material, making way for buildings, roads, and other infrastructure. To ensure the seamless operation of these giants, understanding and maintaining their essential components is paramount. In this comprehensive guide, we will explore the intricate world of excavator parts, their functions, maintenance, and their critical role in construction projects.
The Anatomy of an Excavator
Undercarriage
The undercarriage of an excavator is a critical component that often goes unnoticed, but its importance cannot be overstated. It serves as the foundation upon which the entire machine operates. This section will delve into the undercarriage, highlighting its components, functions, and maintenance.
At its core, the undercarriage consists of tracks, track frames, and various associated components. The tracks are the massive, rugged belts that give the excavator its mobility. They are designed to withstand extreme terrain, providing stability on uneven ground and allowing the machine to move with ease. The track frames support the tracks, distributing the machine’s weight evenly and ensuring proper weight distribution.
The undercarriage components, including rollers, idlers, and sprockets, are essential for smooth operation. Rollers, often referred to as track rollers, are designed to minimize friction and reduce wear on the tracks. They allow the tracks to move smoothly and distribute the weight effectively. Idlers serve as guides for the tracks and are instrumental in maintaining proper tension. Sprockets are the gears that engage with the tracks, driving the machine forward or backward.
To keep the undercarriage in top condition, regular maintenance is paramount. Here are some key aspects of undercarriage maintenance:
- Cleaning: Regularly cleaning the undercarriage to remove dirt, rocks, and debris is essential. Accumulated debris can accelerate wear and tear.
- Lubrication: Proper lubrication of the undercarriage components, including rollers and idlers, is necessary to reduce friction and extend their lifespan.
- Tension Adjustment: Ensuring the tracks are appropriately tensioned is critical. Loose tracks can lead to accelerated wear, while overly tight tracks can strain components.
- Inspections: Regular inspections can identify early signs of wear and damage. Timely replacement of worn components can prevent costly breakdowns.
- Environment Considerations: The undercarriage often operates in harsh environments. Protecting it from corrosive materials and extreme weather conditions can significantly extend its life.
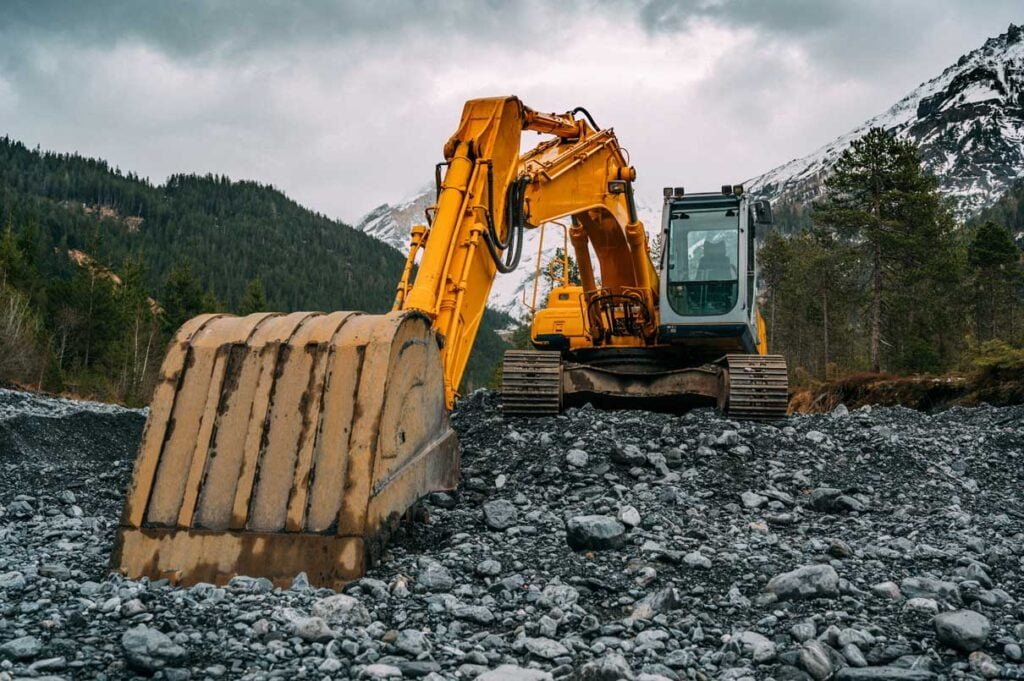
Hydraulic System
The hydraulic system of an excavator is at the heart of its functionality. It plays a pivotal role in powering the machine’s movements, including the extension of the boom, the operation of the arm and bucket, and the smooth flow of hydraulic fluids throughout the system. This section will provide a detailed overview of the hydraulic system, its components, functions, and the significance of proper maintenance.
The hydraulic system operates based on the principles of fluid dynamics. It uses hydraulic fluid, usually hydraulic oil, as the medium to transmit power from one point to another. This system’s primary components include hydraulic hoses, pumps, and cylinders.
1. Hydraulic Hoses: These are the arteries of the hydraulic system, responsible for carrying hydraulic fluid under high pressure. They connect various components and allow for the transfer of energy. Over time, hydraulic hoses can experience wear and tear, leading to leaks or reduced efficiency.
2. Hydraulic Pumps: The hydraulic pump is the heart of the system. It pressurizes the hydraulic fluid, creating the force necessary for the excavator’s movements. The pump is typically powered by the excavator’s engine. Regular maintenance and monitoring of the hydraulic pump’s performance are crucial to ensure smooth operation.
3. Hydraulic Cylinders: These are the muscle of the system. Hydraulic cylinders extend and retract to move the different parts of the excavator, such as the boom, arm, and bucket. Proper maintenance of these cylinders ensures precise and powerful movements.
Maintenance and care of the hydraulic system are vital to keeping the excavator in top working condition. Here are some key aspects of hydraulic system maintenance:
1. Fluid Inspection: Regularly check the hydraulic fluid for contamination, such as dirt or water. Contaminated fluid can damage the system and reduce its efficiency.
2. Filter Replacement: The hydraulic system often includes filters to keep the fluid clean. Periodically replace these filters to ensure a clean and well-functioning system.
3. Hose Inspection: Inspect hydraulic hoses for wear, abrasions, or leaks. Timely replacement of damaged hoses prevents costly issues and maintains system integrity.
4. Hydraulic Fluid Temperature: Be mindful of the hydraulic fluid’s operating temperature. Extremely high or low temperatures can affect the fluid’s performance and the system’s efficiency.
5. Proper Fluid Levels: Ensure that the hydraulic fluid is at the appropriate level. Low fluid levels can lead to cavitation, which can damage the pump.

Engine and Transmission
The engine and transmission of an excavator are two essential components that work together to provide the machine with the power and mobility it needs to carry out a wide range of tasks. In this section, we will take an in-depth look at the engine and transmission, their functions, and the significance of proper maintenance.
1. Engine: The engine is the powerhouse of the excavator. It is responsible for generating the mechanical energy needed to drive the machine’s various functions. Most excavators are equipped with diesel engines due to their durability and high torque characteristics.
The engine’s tasks include providing power to hydraulic pumps, which in turn control the movement of the boom, arm, and bucket. It also powers other auxiliary systems, such as cooling and filtration. Proper maintenance of the engine is crucial for ensuring consistent performance.
Maintenance of the excavator’s engine involves the following:
- Regular Oil Changes: Periodic oil changes are essential to maintain engine lubrication and prevent overheating. It’s crucial to use the recommended oil grade.
- Filter Replacement: Air, fuel, and oil filters should be replaced at specified intervals to ensure a clean and efficient engine operation.
- Cooling System Maintenance: The engine’s cooling system must be inspected to avoid overheating. Coolant levels and the condition of radiator fins should be regularly checked.
- Exhaust System Inspection: Regularly inspect the exhaust system to ensure proper emission control and to identify any signs of damage or leaks.
2. Transmission: The transmission is responsible for controlling the speed and direction of the excavator. It converts the engine’s power into rotational force, which drives the tracks and allows the machine to move forward or backward.
Maintenance of the transmission is vital for ensuring the excavator’s mobility and control. The following points should be considered:
- Fluid Level Checks: Regularly inspect the transmission fluid levels and replace it as needed. Low fluid levels can lead to transmission damage.
- Filter Replacement: Similar to the engine, the transmission also has filters that need periodic replacement to maintain the cleanliness of the transmission fluid.
- Gearing Inspection: Regularly inspect the transmission gears and other components for signs of wear or damage. Addressing these issues promptly can prevent costly repairs.
- Seal and Gasket Inspection: Inspect the seals and gaskets in the transmission system for leaks or damage. Addressing these issues is crucial to prevent fluid loss.

Bucket and Attachments
The bucket and attachments of an excavator are the business end of the machine, where the actual digging, lifting, and material handling occur. In this section, we will explore the bucket and attachments, their types, functions, and the importance of proper maintenance.
1. The Bucket: The bucket is the primary attachment on an excavator, and it comes in various shapes and sizes to suit different tasks. It is responsible for digging, scooping, and moving materials, making it a versatile tool for construction and excavation.
Types of buckets include:
- Digging Bucket: This is the standard bucket used for digging trenches and excavating soil and other materials.
- Rock Bucket: Designed with reinforced structure and sharp teeth, the rock bucket is used for digging in hard and rocky terrain.
- Ditching Bucket: A wider and shallower bucket that’s ideal for creating ditches, grading, and leveling.
- Cleanup Bucket: With a larger capacity and often a smooth edge, this bucket is used for handling loose materials, such as sand, gravel, or debris.
Proper maintenance of the bucket is essential for optimal performance. This includes:
- Tooth Inspection: Regularly inspect the bucket teeth for wear and damage. Replacing worn teeth ensures efficient digging.
- Cutting Edge Maintenance: Keep the cutting edge sharp to improve digging performance and minimize wear on the bucket.
- Lubrication: Grease or lubricate pivot points and joints to prevent corrosion and maintain smooth movement.
2. Attachments: Excavators can be equipped with various attachments to expand their functionality. These attachments can be easily swapped out to adapt the machine for different tasks. Common attachments include:
- Hydraulic Hammers: Used for breaking rock or concrete.
- Augers: For drilling holes, often used in foundation work or installing utility poles.
- Grapples: These are used for handling logs, rocks, or other irregularly shaped objects.
- Rippers: Designed for breaking up hard surfaces or compacted soil.
- Compactors: Used for compacting soil or other materials to create a solid foundation.
Maintenance of attachments is as crucial as that of the bucket. This involves:
- Regular Inspection: Inspect the attachment for signs of wear, damage, or loose components.
- Hydraulic System Check: Ensure that the hydraulic connections and hoses for the attachments are in good condition.
- Lubrication: Grease or lubricate attachment joints and pivot points to maintain smooth operation.
- Proper Storage: Store attachments correctly to prevent rust and damage when not in use.
Maintenance and Care
Routine Inspections
Regular inspections of the excavator’s various components are essential to identify wear and tear early. Timely replacement or repair of worn parts can prevent costly breakdowns and downtime.
Lubrication
Proper lubrication of moving parts, especially within the hydraulic system, is vital to reduce friction, extend the lifespan of components, and maintain the excavator’s overall efficiency.
Cleaning
Keeping the excavator clean from dirt, debris, and corrosive materials can prevent damage to sensitive parts and maintain its appearance, which can be a point of pride for operators and owners.
Storage
Proper storage during periods of inactivity helps protect the excavator from the elements and potential theft or vandalism. It’s an essential aspect of long-term maintenance.
Sourcing Excavator Parts
OEM vs. Aftermarket
When it comes to replacing parts, one must decide between Original Equipment Manufacturer (OEM) and aftermarket parts. OEM parts are manufactured by the excavator’s maker, ensuring a precise fit, but often come at a premium price. Aftermarket parts, on the other hand, are more cost-effective but may vary in quality and warranty.
Reliable Suppliers
Choosing reputable suppliers is crucial to ensure the quality and authenticity of the parts. Research, read reviews, and ask for recommendations to identify reliable sources.
Importance of Excavator Parts
Enhanced Performance
Proper maintenance and regular replacement of worn parts enhance the excavator’s performance, leading to increased productivity and a smoother operation.
Safety
Well-maintained excavator parts reduce the risk of accidents, ensuring a safe working environment for operators and those in close proximity to the machine.
Cost Savings
Preventive maintenance and timely part replacements are cost-effective in the long run, preventing major breakdowns that can be expensive to repair and cause project delays.
Environmental Impact
Proper maintenance reduces the environmental footprint by minimizing waste and the need for new manufacturing. It’s a step toward sustainability in construction.
Conclusion
In conclusion, excavator parts are the unsung heroes behind every successful construction project. Regular maintenance and careful consideration when sourcing parts are paramount to the excavator’s longevity, efficiency, and your construction project’s success.
Frequently Asked Questions
1. How often should I inspect my excavator’s parts?
Regular inspections should be carried out at least every 250 operating hours or as recommended by the manufacturer.
2. Are aftermarket parts as reliable as OEM parts?
The reliability of aftermarket parts varies, but many reputable aftermarket suppliers offer high-quality components at a more affordable price.
3. What are the signs that my excavator parts need replacement?
Signs of wear, reduced performance, and unusual noises are indicators that parts may need replacement.
4. Can I perform excavator maintenance myself?
Basic maintenance tasks like cleaning and lubrication can be done by operators, but more complex tasks should be left to trained technicians.
5. How can I find reliable suppliers for excavator parts?
Research online reviews, ask for recommendations within your industry, and verify the supplier’s reputation and authenticity before making a purchase.