Introduction
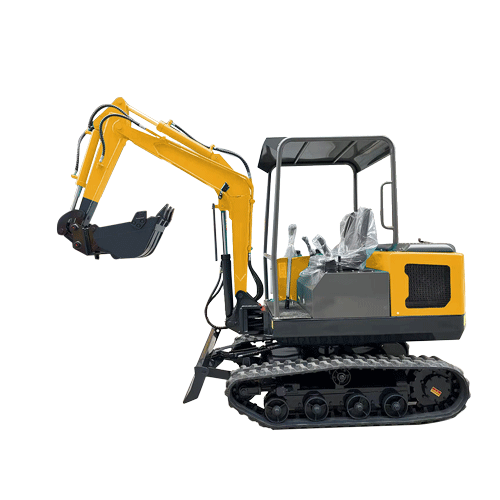
In the world of heavy machinery, excavators stand as indispensable tools for various construction, mining, and excavation projects. These versatile machines rely heavily on their tracks for mobility and stability, making the choice of tracks a critical decision. In this blog post, we delve into the significance of opting for high-quality tracks for excavators and explore how they can enhance performance, durability, and overall efficiency.
Understanding the Role of Tracks in Excavator Operations
Before delving into the significance of high-quality tracks, it’s crucial to grasp the pivotal role they play in the operations of excavators. Beyond merely facilitating movement, tracks serve as the backbone of excavator functionality, influencing every aspect of its performance. They provide essential traction on a variety of terrains, ranging from soft soil to rugged landscapes, ensuring the excavator maintains stability and maneuverability across diverse work environments. Additionally, tracks play a critical role in evenly distributing the machine’s weight, minimizing ground pressure and preventing soil compaction, particularly in sensitive or environmentally protected areas. In essence, tracks serve as the foundation for achieving smooth and efficient excavator operations, making their quality and integrity paramount to the machine’s overall functionality and productivity.
The Impact of Track Quality on Excavator Performance
The quality of tracks has a profound impact on the performance of excavators across multiple dimensions, including speed, maneuverability, and productivity. When equipped with inferior tracks, excavators may encounter issues such as slippage, diminished traction, and heightened susceptibility to wear and tear. These shortcomings can translate into increased downtime and reduced operational efficiency, ultimately hampering productivity on the job site.
In contrast, high-quality tracks present a stark contrast by offering superior grip, stability, and durability. They effectively mitigate the risks associated with subpar tracks, allowing excavators to navigate diverse terrains with confidence and precision. With enhanced traction and stability, excavators equipped with high-quality tracks can maintain optimal performance levels even in challenging conditions, maximizing productivity and minimizing disruptions.
Factors to Consider When Choosing Tracks for Excavators
Selecting the right tracks for excavators involves considering several factors, including track type, tread pattern, material composition, and size. Each of these factors contributes to the overall performance and longevity of the tracks, making informed decision-making essential for maximizing excavator efficiency and minimizing maintenance costs.
Factors for Consideration | Description |
---|---|
Track Type | – Rubber tracks: Versatile, provide traction on various terrains. |
– Steel tracks: Durable, suitable for heavy-duty applications and rough terrain. | |
Tread Pattern | – Deep treads: Enhanced grip, ideal for muddy or soft soil conditions. |
– Chevron treads: Provide stability and traction on uneven or rocky terrain. | |
Material Composition | – Rubber tracks: Made of high-quality rubber compounds for durability and flexibility. |
– Steel tracks: Constructed from reinforced steel for superior strength and longevity. | |
Size | – Track width: Determines the stability and weight distribution of the excavator. |
– Track length: Impacts the surface area in contact with the ground, affecting traction and stability. |
Benefits of Investing in High-Quality Tracks
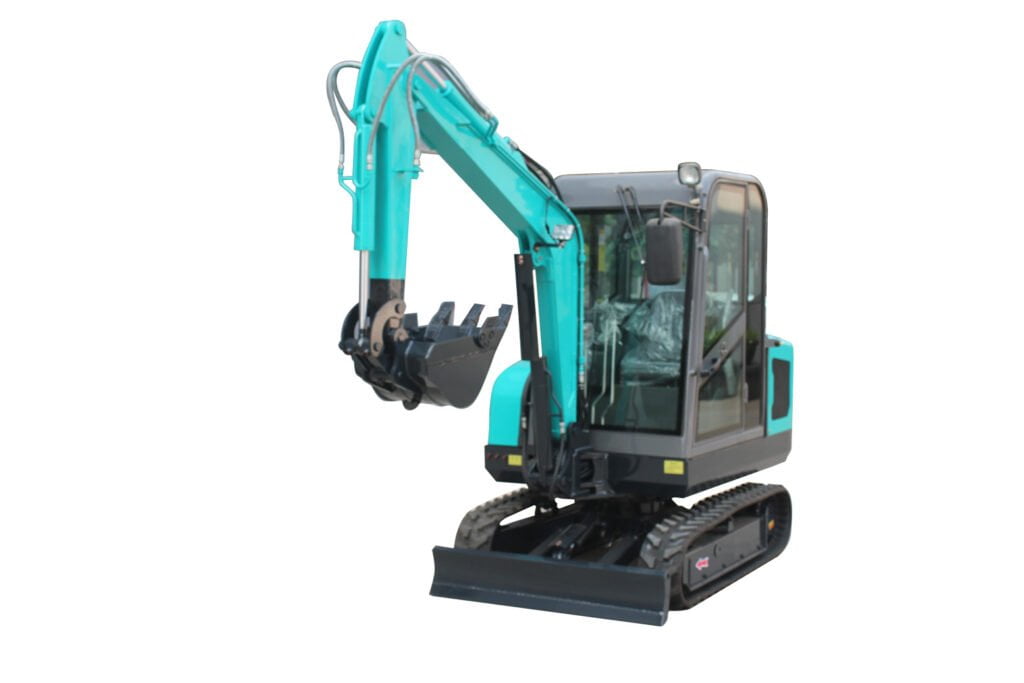
Investing in high-quality tracks for excavators yields numerous benefits for operators and contractors. These include extended track life, reduced downtime, enhanced operator safety, improved fuel efficiency, and ultimately, higher returns on investment. By prioritizing track quality, businesses can optimize their excavator operations and achieve greater productivity and profitability.
Case Studies: Real-World Examples of High-Quality Tracks in Action
To underscore the significance of opting for high-quality tracks, we provide compelling case studies featuring real-world instances of excavators outfitted with top-tier tracks. These case studies offer tangible evidence of the advantages enjoyed by operators, including heightened productivity, diminished maintenance expenses, and accelerated project schedules.
In one instance, a construction company upgraded its excavator fleet with premium tracks, resulting in a noticeable uptick in productivity. The enhanced traction and stability provided by the high-quality tracks allowed operators to maneuver more efficiently across various terrains, thereby completing tasks in less time.
Conclusion
In conclusion, high-quality tracks are essential components of excavators that significantly impact their performance, durability, and overall efficiency. By understanding the importance of investing in top-notch tracks and considering key factors when selecting them, operators and contractors can optimize their excavator operations and achieve superior results.
FAQ
What are the main types of tracks available for excavators?
Excavators typically use two main types of tracks: rubber tracks and steel tracks. Rubber tracks are preferred for their versatility, providing traction on various terrains while minimizing damage to surfaces. Steel tracks offer superior durability and are well-suited for heavy-duty applications and rough terrain.
How do I know if it’s time to replace my excavator tracks?
Signs that indicate the need for track replacement include excessive wear, visible damage such as cuts or tears, reduced traction, and increased track slippage. Regular inspections and monitoring of track condition can help identify issues early and prevent costly downtime.
Can I retrofit my existing excavator with high-quality tracks?
Yes, it is often possible to retrofit existing excavators with high-quality tracks. However, compatibility and proper installation are crucial considerations. Consult with a qualified technician or dealer to ensure the selected tracks are compatible with your excavator model and meet your specific operational requirements.